The Tragic Story of Aisha Muhammed
It was 12:35 pm on a hot and humid day. Musa had been feeling ill for several days and his wife, Aisha, was growing increasingly worried. She decided to take him to the local health clinic to seek medical attention.
When they arrived at the clinic, Aisha was shocked to find that the shelves were empty. The clinic had run out of the medicine that Musa needed. The nearest hospital was miles away and they didn’t have a vehicle to take him there.
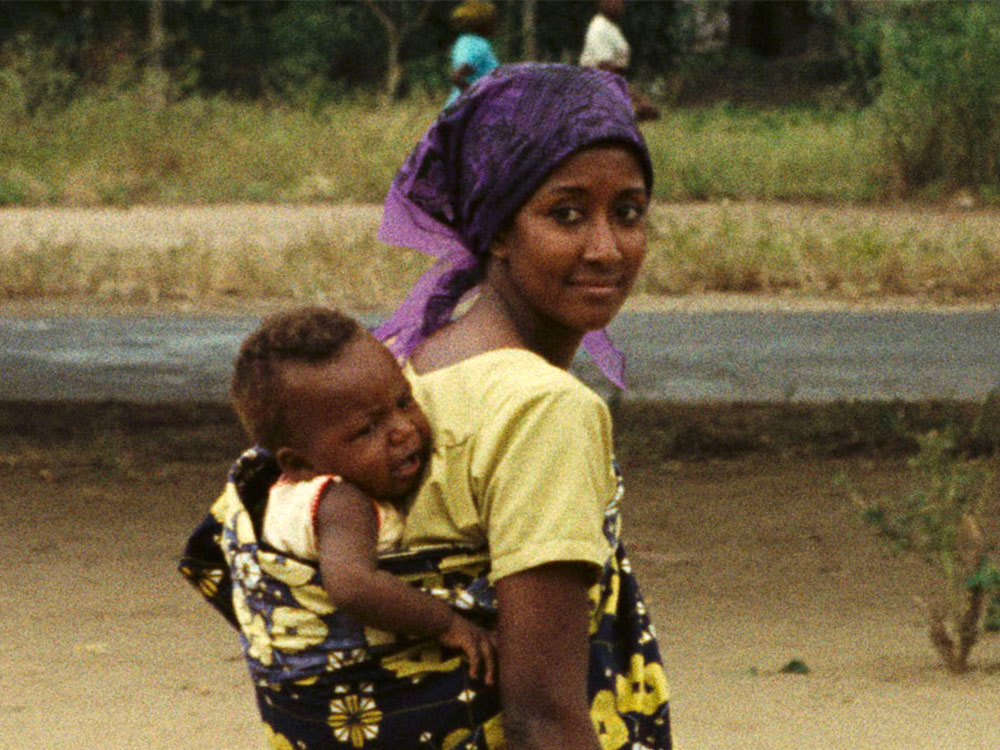
Aisha pleaded with the clinic staff to help her husband, but they could do nothing without the medicine. She watched helplessly as Musa’s condition deteriorated before her eyes. He was coughing violently and struggling to breathe.
Aisha knew that time was running out, so she made the difficult decision to carry Musa on her back and walk the long journey to the hospital. It was a grueling trek in the scorching heat, but Aisha was determined to save her husband’s life.
However, when they finally arrived at the hospital, they were met with another devastating blow. The hospital had also run out of the medicine that Musa needed. Aisha was beside herself with grief and desperation.
Musa’s condition continued to worsen and he passed away that evening. How could things have gone so terribly wrong?
Why are Inventory Stock Outs of Medicines Still A Problem Today?
It wasn’t until later that Aisha learned the cause of her husband’s death. The medicine that Musa needed had been out of stock for several weeks, but the local clinic and hospital had failed to restock in time. It was a tragedy that could have been prevented, and Aisha was left to bear the consequences of the lack of access to essential medicines.
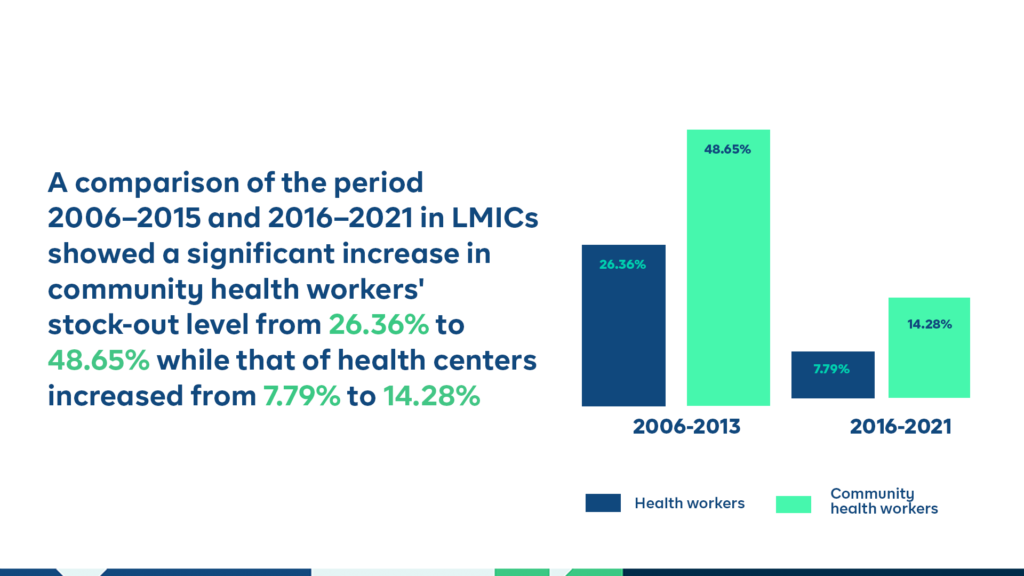
Stock-outs of medicines across the entire pharma supply chain can occur due to a variety of reasons. Some of the most common reasons include a lack of proper inventory management, inaccurate forecasting, inadequate production capacity, and unforeseen demand spikes. In addition, supply chain disruptions caused by natural disasters, global pandemics, or transportation disruptions can also contribute to stock-outs.
In many cases, the root cause of stock-outs is the lack of visibility and transparency across the supply chain. Different stakeholders in the supply chain may be using different systems or not communicating effectively with each other, which can lead to delays, inaccuracies, and inefficiencies in the supply chain. This lack of visibility and communication can make it difficult to identify potential stock-out situations and take corrective action in a timely manner.
How To Stop Inventory Stock Outs With Your Traceability Software
However, with the use of an en-to-end traceability and serialization software that connects the entire supply chain, it is possible to take practical steps to mitigate the problem of stock-outs. Here are the three most important steps
1. Get Everyone on Board with the Technology/Standard
One of the first steps in stopping stockouts with traceability is to make sure everyone across the chain agrees to use one standard for their data management processes. This includes manufacturers, distributors, donors, hospitals, and pharmacies. By having everyone in the supply chain using the same system, it is possible to ensure that everyone is working with the same information, which can help to prevent stock-outs from occurring.
A lot of progress has been made in this regard with the GS1 EPCIS standard being the widely accepted standard for serializing products and enabling traceability. To utilize this standard, any traceability solution you choose to go with must be a GS1 Solution Partner.
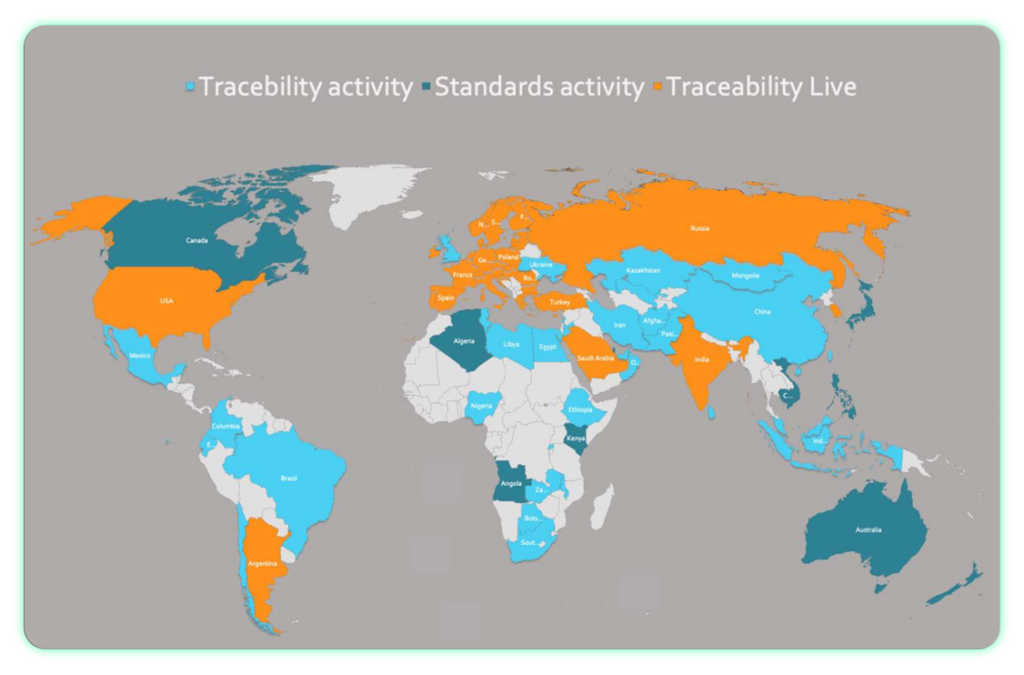
2. Integrate with Inventory & Distribution Management Systems
Just because everyone agrees to use the same standard doesn’t automatically mean all the different inventory data silos are now connected.
Another important step is to integrate with the inventory management systems used by all players in the supply chain as well as order/fulfillment software, and even full-scale ERPs. This allows for the seamless transfer of data between the two systems, providing real-time visibility into inventory levels and enabling more accurate forecasting and replenishment. By having access to this data, manufacturers can quickly identify and address potential stock-out situations, minimizing the impact on patients.
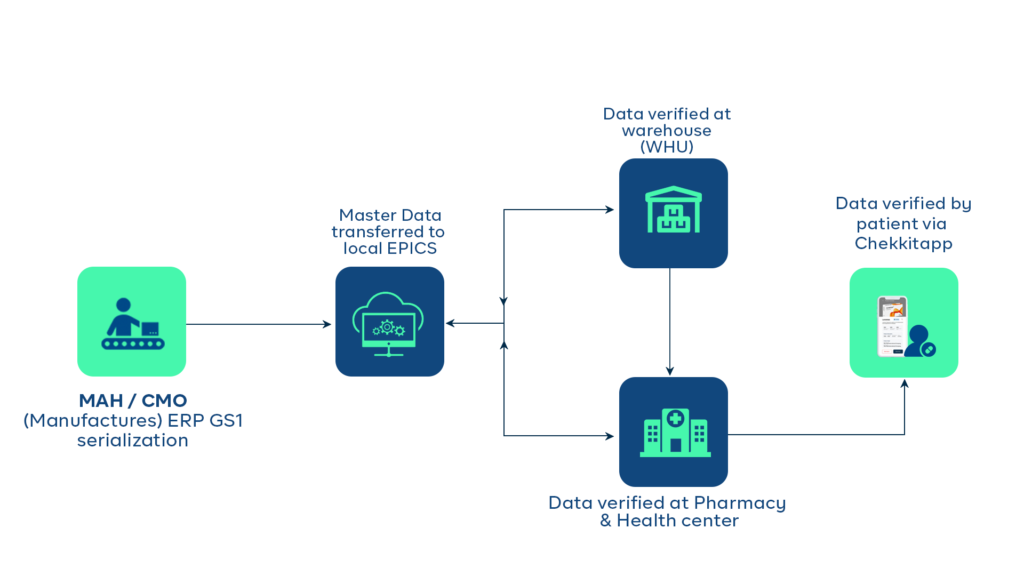
3. Integrate with POS Machines for Real-Time Sales Data
POS machines can also be integrated with the pharma traceability and serialization software to provide real-time visibility into sales data at the pharmacy level. This allows for more accurate forecasting and replenishment, as well as the ability to automatically update inventory across the entire supply chain immediately after the medicine is sold. By having access to this data, manufacturers can work with pharmacies to ensure that they have the inventory they need to meet patient demand.
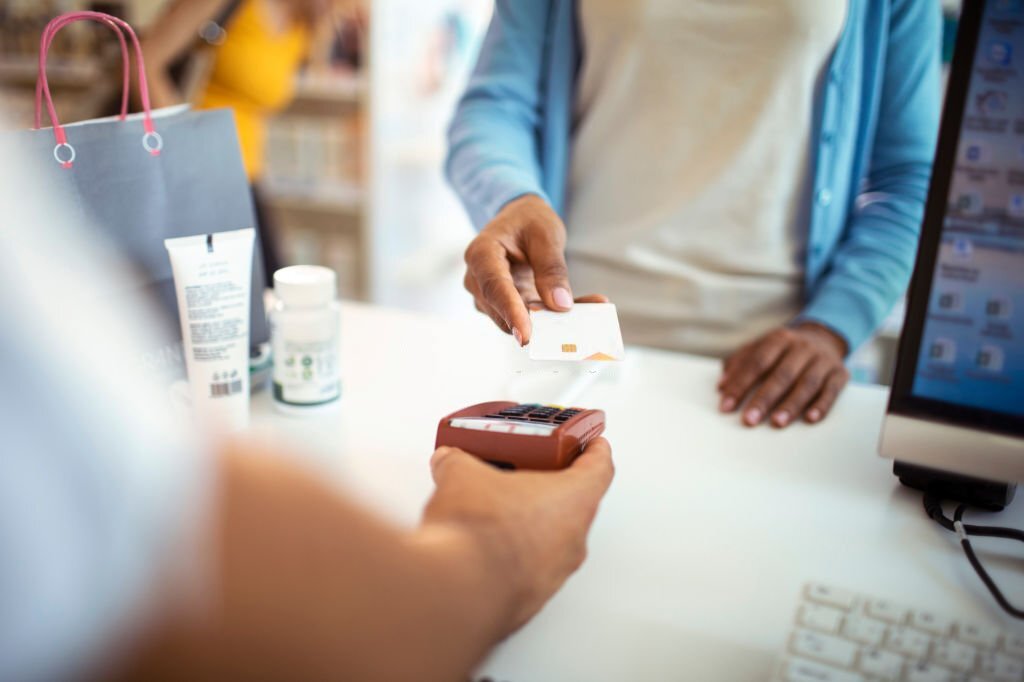
How Does Chekkit Prevent Inventory Stock Outs By Connecting The Entire Supply Chain?
Before now, integrating with all the different software used by the different supply chain stakeholders with the GS1 standard was non-existent. There are different solutions that already use the GS1 standard but the sharing of information between these systems were very limited.
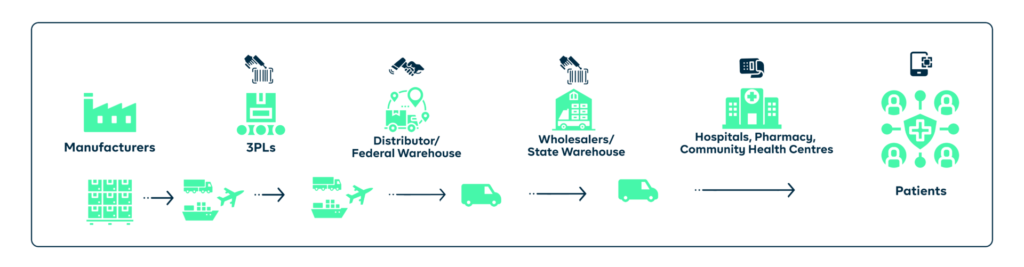
This is where Chekkit’s traceability infrastructure comes in. You can manage inventory across different warehouses, and locations by integrating with the inventory tools already being utilized by these different locations without having to change their processes. For locations that do not have functional inventory systems, they can immediately start digitally managing their operations by using our in-built inventory management system.
Integrating chekkit means being able to read and utilize the mandatory GS1-standard serialized codes that are already on drug packaging globally.
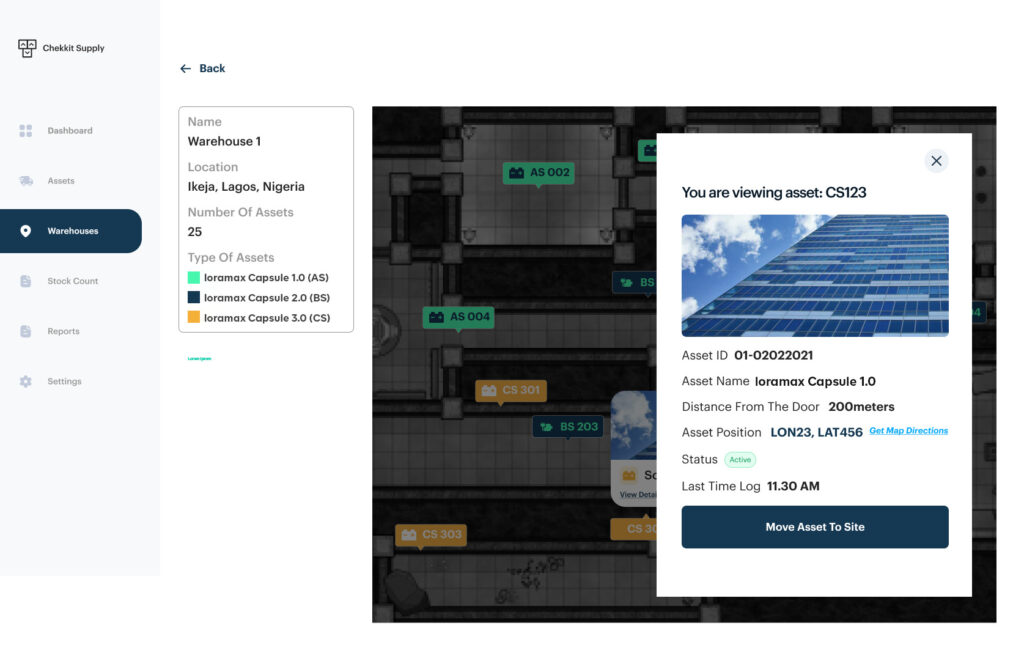
If you’re interested in learning more about how traceability solutions can help you stop inventory stock outs of essential medicines, feel free to request a demo of our traceability software today!
As a pharmaceutical manufacturer, supply chain manager, or logistics expert, this technology could help you stay ahead of the curve and ensure that your products reach patients safely and efficiently.